Исследование защитно-диффузионных свойств покрытий
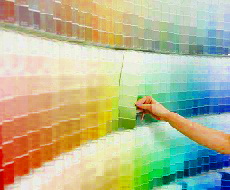
Лакокрасочные покрытия не могут полностью изолировать окрашенную поверхность металлов от воздействия коррозионно-активных молекул воды, кислорода, агрессивных газов. Информацию о проницаемости покрытий для различных агрессивных веществ и о состоянии поверхности металла под лакокрасочными пленками можно получить, используя электрохимические и электрические методы исследования, например определение электрохимического потенциала металла, измерение импеданса покрытия или его сопротивления (при контакте с электролитом) прохождению постоянного и переменного токов.
Электрическое сопротивление лакокрасочных пленок, контактирующих с электролитом, характеризует их способность служить диффузионным барьером на пути движения ионов электролита и молекул воды к поверхности металла, а изменение емкости той же системы позволяет оценить набухание пленок. Поэтому измерение указанных показателей все более широко применяется для оценки защитно-диффузионных свойств покрытий и их сплошности. В обзоре приведено много примеров использования электрических методов при изучении защитной способности покрытий различных химической природы и состава. Так, электрические методы применяли при исследовании пассивирующих и протекторных свойств грунтов и защитных свойств комплексных покрытий. Импедансометрический метод (измерение полного сопротивления) целесообразно использовать при выборе соотношения смола - отвердитель и оптимального содержания пигментов для достижения длительного защитного действия. Хорошие результаты получены этим методом при определении стойкости противокоррозионных покрытий к перепаду температур.
При исследовании защитных свойств покрытий на рулонных металлах установлено, что момент начала разрушения пленок соответствует перегибу на кривой зависимости полного сопротивления от частоты.
Эти методы дают возможность исследовать структуру тонкослойных конверсионных фосфатных и хроматных слоев, водо и ионопроницаемость покрытий на металле и влияние на них дефектов пленок, характер протекания коррозионных процессов при различных воздействиях, механизм защитного действия некоторых пленкообразователей.
Частным случаем импедансометрии является емкостно-омический метод, основанный на определении емкости С и сопротивления R сэндвича - металл - покрытие - электролит, который стал применяться в исследовательской практике более четверти века назад. Возможности этого метода расширились за счет анализа кинетики изменения частотной дисперсиий в ходе воздействия на покрытие агрессивных жидких сред.Как видно из приведенных данных, как и в начале испытания, так и через 15 сут, величина R образцов с ростом частоты переменного тока уменьшается, а величина С практически не зависит от частоты. Это характерно для качественных покрытий, поскольку значение K~l/(2Jt/Ctg6), и для полимеров в стеклообразном состоянии с ростом / в указанных пределах величина tg6 изменяется мало.
В противоположном случае при испытаниях пористых покрытий сопротивление пленок на несколько порядков ниже и не зааисит см частоты, поскольку определяется в основном высокой проводимостью электролита, а абсолютная величина емкости покрытий заметно выще полученных значений и сильно зависит от частоты. Установлено, что высокие значения емкости соответствуют низким защитным свойствам покрытий.
Стабильность частотной зависимости и малое изменение величин R и С указывает на то, что в данной среде за время испытаний эти покрытия не разрушаются и сохраняют защитное действие.
G применением емкостно-омического Метода были исследованы противокоррозионные свойства топливостойких покрытий, применяемых для защиты судовых танков и цистерн при погружении в воду, 3%-й раствор хлорида натрия, авиационное топливо, автомобильный бензин А-76[1б0]. По убыванию стойкости покрытий к воздействию пресной воды исследованные эмали расположены в следующей последовательности: Б-ЭП-68>Б-ЭП-65>Б-ЭП-421>ЭП-755; солестойкость покрытий выше водостойкости и примерно одинакова для всех эмалей. При погружении покрытий в углеводородные топлива они проявляют высокие защитные свойства.
В торможении электродных процессов на окрашенном металле важное значение имеет электрическое сопротивление пленки, поскольку в коррозионном электрохимическом элементе лакокрасочная пленка выполняет роль внутренней цепи, где происходит перенос ионов электролита.
Электрическое сопротивление сухих пленок достаточно велико, что препятствует возникновению коррозии. При погружении в раствор электролита сопротивление пленок снижается. Ниже приведены данные по относительному изменению электрического сопротивления полимерных пленок толщиной 35 мкм при погружении в 0,5 н.раствор сульфата натрия - исходное сопротивление, Я15 - сопротивление через 15 сут.)
Пленкообразователь
Льняное масло Нитрат целлюлозы А лкидно-сти рольный олигомер Поливинилбутираль
Скорость изменения и конечное значение электрического сопротивления зависят от природы пленкообразователя, присутствия гидрофильных групп (особенно способных к ионному обмену), а также от характера электролита. С увеличением pH среды происходит замена водорода в карбоксильных группах пленки на более легко ионизирующиеся атомы щелочного металла, что приводит к гидрофилизации пленки, резкому увеличению водопоглощения и электрической проводимости покрытия. Например, защитная способность масляных покрытий в щелочных средах крайне низкая.
В отличие от гидрофильных пленок, покрытия, образованные гидрофобными пленкообразователями, в частности эпоксидными или хлорсодержащими сополимерами, способны длительное время сохранять высокое электрическое сопротивление и тем самым препятствовать развитию коррозионного процесса. Проводимость таких покрытий может возникнуть лишь в результате наличия сквозных пор, заполняемых электролитом, или появления дефектов. Подобным дефектом может явиться поверхность раздела связующее - дисперсный наполнитель. Из приведенных данных видно также изменение величин 1/Р, где р- паропроницаемостъ свободных пленок [в кг/(м-с*Па)].
Наполнение приводит к снижению устойчивости покрытий при Контакте с электролитом. Наименьшее изменение R за 15 сут. воздействия и наименьшая проницаемость пленок для водяного пара наблюдаются при ОСП, равном 20%. При дальнейшем росте ОСП устойчивость покрытий заметно снижается, что объясняется превышением критического содержания, когда пленкообразователя не хватает для создания сплошной оболочки вокруг частиц наполнителя, и перенос молекул воды и ионов происходит в основном по границам раздела и порам пленки.
Метод определения сопротивления предложено использовать для оценки продолжительности эксплуатации до потери защитной способности покрытий (эпоксидных, полиэфирных и т.п.), первоначально имеющих хорошую адгезию к подложке.
Кривая зависимости электрического сопротивления от продолжительности воздействия агрессивной среды имеет три участка, соответствующих различным стадиям процесса разрушения покрытия (рис.). Вид кривой не зависит от механизма разрушения. На первой стадии наблюдается сравнительно быстрое уменьшение сопротивления вследствие диффузии агрессивных агентов, прежде всего воды с растворенным кислородом, и увеличения их содержания в пленке. На второй стадии величина электрического сопротивления стабилизируется или очень медленно снижается. На этой стадии может происходить химическое взаимодействие агрессивной среды с материалом пленки или подпленочная коррозия; при этом сплошность пленки не нарушена. На третьей стадии сопротивление снова резко снижается, что указывает на нарушение целостности покрытия. Сопротивление при этом снижается до определенной (для данного материала и выбранной агрессивной среды) минимальной величины, при которой происходит разрушение покрытия.
В случае испытания толстослойных покрытий или систем лакокрасочного покрытия изменение сопротивления происходит иногда в течение многих месяцев. Например, химическую стойкость покрытий, предназначенных для защиты сетевых труб системы подземного выщелачивания урановых руд, оценивали по изменению сопротивления в течение года.
На рис. представлены кривые изменения сопротивления различных покрытий в период воздействия на них 5%-го раствора серной кислоты при 20 °С. Видно, что из разных лакокрасочных композиций формируются покрытия, которые заметно отличаются как по величине начального сопротивления, так и по интенсивности его изменения в ходе длительного воздействия агрессивной среды.
Низкое электрическое сопротивление покрытия обусловливает проникновение в покрытие молекул воды и ионов, легкое перемещение ионов сквозь покрытие и возникновение реакций с ионным переносом (коррозия) на границе раздела металла и полимера. При измерении сопротивления последствия протекания всех перечисленных процессов интегрируются. Однако эти измерения не дают информации о том, какое из явлений регулирует или лимитирует коррозионный процесс.
При измерениях в режиме постоянного тока основной вклад в величину R вносит не омическое, а поляризационное сопротивление. Имеются методы раздельного определения этих составляющих, причем хорошие защитные свойства проявляются у покрытий с высоким поляризационным сопротивлением. При измерении в режиме переменного тока (400-1000 Гц) поляризационное сопротивление также составляет определенную долю общего сопротивления.
Измерения емкости позволяют без разрушения образца определить количество воды в покрытии.Сравнивая результаты определения содержания воды по данным измерений емкости Хэл и гравиметрического метода Хгр- получают информацию о путях проникновения и способе распределения воды. Если хэ„/ Хгр = 1. это указывает ка равномерное распределение воды; Хэп/Хгр<1 указывает на скопление воды в порах пленки или капиллярах; Хэп/Хгр>1 трактуется как слоевое распределение воды, например в результате нарушения межслойной адгезии, или на границе пленка - металл. Преимуществом метода является быстрота определения, хорошая воспроизводимость, возможность определения малого количества воды, проникающей в начальный период. Полагают, что измерения емкости с большей точностью характеризуют коррозионную стойкость покрытия по сравнению с гравиметрическим методом, поскольку решающим фактором является не само присутствие воды, а его влияние на электрические свойства покрытий, которые с помощью современной техники могут быть измерены весьма точно электропроводности дает сочетание контроля данных параметров е другими современными физико-химическими методами. Например, исследуя термостарение фенолоформальдегидных пленок, сочетали непрерывное измерение объемной проводимости с масс-спектромет- рией и термогравиметрией и установили, что при температуре экстремума электропроводности наблюдается резкое увеличение потерь массы образца.
Была разработана установка для исследования термостарения пленок при контроле е' и tgfi с одновременным проведением дифференциального термического анализа.С целью выбора отвердителя лака для защиты паяного шва металлической консервной тары исследовано влияние строения фенолоформальдегидных олигомеров на термостойкость эпоксидно-фенольных покрытий. Отвердителями смолы Э-05к служили фенольные смолы резольного типа — продукты конденсации формальдегида с фенолом и n-грег-бутилфенолом (ФПФ-1), с фенолом и о-крезолом (ФКоФ-4), а также смесь ФПФ-1 с ФКоФ-4 в соотношении 1:1.
Зависимость параметра Atge/tgjS от продолжительности старения покрытий при 200 °С показана на рис.Здесь Atg6 = tgT6 - tg06 - абсолютное изменение tg6 покрытий за т часов. Видно, что у всех покрытий в течение первого часа выдержки при 200 °С происходит интенсивное изменение уровня диэлектрических потерь, вероятно, обусловленное протеканием процессов доотверждения. В ходе дальнейшей выдержки покрытий, полученных с ФПФ-1 или ФКоФ-4, начинает проявляться все более резкое изменение tg6, тогда как в случае образцов, отвержденных смесью этих резолов, уровень диэлектрических потерь сохраняется неизменным в течение последующего времени наблюдения.Результаты, полученные при использовании обоих методов, хорошо согласуются.Таким образом, описываемые методы могут успешно применяться и для исследования старения покрытий при натурных или ускоренных испытаниях.