Поверхностные и объемные свойства материалов при производстве радиоэлектронных средств
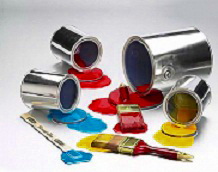
Поверхностные явления оказывают большое влияние на эксплуатационные характеристики ЛКП, в том числе применяемых в производстве РЭС, и это достаточно широко освещено в литературе. В то же время проблема зависимости качества получаемых покрытий от поверхностных и объемных свойств материалов ПП и ЭМ не отражена в литературе. Под поверхностными свойствами материалов понимают физическое и химическое состояние поверхностного слоя изделия, включая шероховатость, смачиваемость, удельное поверхностное электрическое сопротивление, состав и содержание технологических загрязнений, наличие дефектов, появившихся в процессе изготовления изделия и т. д. Для металлов и сплавов, кроме того, необходимо принимать во внимание такие характеристики как электродный потенциал, энергия активации,микро твёрдость наружного слоя и пр. Под объемными свойствами понимают плотность, макро- и микроструктуру, удельное объемное электрическое сопротивление, теплофизические характеристики (теплоемкость, тепло- и температуропроводность), газосодержание в системе и т. д. Для ПП и ЭМ эта проблема усложняется конструктивно-технологическими особенностями изделий, в состав которых входят детали из различных диэлектриков, металлов и сплавов [стеклотекстолитовые, керамические, печатные проводники, металлические электро-радиоэлементы (ЭРЭ), контактные выводы, крепежные детали].Вначале рассмотрим основные характеристики широко применяемых для изготовления ПП фольгированных диэлектриков. В отечественной промышленности используется стеклотекстолит марок СТФ, ФТС, СТЭК, СТНФ, СФ, СФ-2Н, СТПА. Основой любого стеклотекстолита является, как правило, аппретированная стеклоткань (подвергнутая или не подвергнутая термохимической обработке), пропитанная связующим на основе эпоксидных смол, и медная фольга. В результате многочисленных технологических операций производства фольгированных диэлектриков (особенно при покрытии волокна замасливателем, пропитке стеклоткани, сборке пакетов, прессовании) возможно появление следующих дефектов: образование „газовых мешков” и полостей, адсорбция примесей из окружающей среды и проникновение их в глубь материала, наличие непропитанных участков стеклоткани, присутствие механических включений, проявление текстуры, локальное побеление стеклоткани после кипячения в воде или выдержки в припое.
За рубежом в производстве фольгированных диэлектриков начинают широко применять полимеры с высокой температурой стеклования (около 200 °С), вакуумные процессы пропитки и прессования. Работы в этом направлении проводятся и в СССР. В частности, ведется разработка фольгированного диэлектрика на основе полимеров с узким молекулярно-массовым распределением (MMP'i. С целью повышения качества ПП, для обеспечения полной полимеризации связующего и уменьшения газосодержания в системе на многих предприятиях-потребителях проводят термо-стабилизацию заготовок ГШ при температуре 170 °С в течение 15 ч. В технические условия на стеклотекстолит марки СТФ введен показатель — кипячение образца в дистиллированной воде,
В табл. приведены сравнительные характеристики отечественного диэлектрика марки СТФ и зарубежных аналогов. Как видно из таблицы, отечественный диэлектрик уступает зарубежным по таким важнейшим поверхностным показателям, как сопротивление изоляции, удельное поверхностное электрическое сопротивление, стойкость к расплавленному припою, испытание на „миэлинг”, а также и по объемным показателям — водо-поглощению, удельному объемному электрическому сопротивлению. По нашему мнению, это связано не только с качеством исходных компонентов стеклотекстолита (в частности, температура стеклования зарубежных связующих на 50—100 °С выше, чем у эпоксидной смолы, применяемой для получения диэлектрика), но и с равномерностью распределения связующего во всем объеме стеклоткани при соотношении связующее : стеклоткань с наполнителем & 2 :1. Если выполняются эти условия, обеспечиваются максимальная степень сшивания связующего и высокая его адгезия к стеклоткани и, следовательно, технологические воздействия не должны вызывать оголения текстуры и вымывания связующего.
В отечественной практике производства ПП и ЭМ после травления медной фольги на связующее и стеклоткань приходится более 20 механо-химических и термических технологических воздействий, в том числе загрязнение при хранении ПП в производственных условиях до влагозащиты в течение 7-15 сут. При этих воздействиях может происходить вымывание связующего, оголение текстуры и адсорбция трудноудаляемых технологических загрязнений.
Нередко в стеклотекстолите содержится значительное количество газов. Перед ответственными технологическими операциями необходимо обязательно проводить дегазацию заготовок, деталей, изделий путем термо-стабилизации, термо-тренировки, вакуумирования, сушки. В табл. приведены регламентированные режимы термо-тренировки изделий из стеклотекстолита в зависимости от их массы и толщины материала (ОСТ 107.9.4001—88). Как видно из табл. с увеличением толщины материала изделия и, следовательно, его массы возрастает продолжительность процесса диффузии газов из объема и стабилизации свойств материала. Для ускорения этих процессов увеличивают время сушки ЭМ после обезжиривания непосредственно перед влагозащитой до 2-4 ч, вместо 0,5-1 ч (ОСТ 4Г0.054.205).
Хотя малое число публикаций и экспериментальных данных не позволяет однозначно установить зависимость надежности и долговечности покрытий на ПП и ЭМ от поверхностных и объемных свойств фольгированных диэлектриков, с определенными допущениями судить о ней можно по аналогичной зависимости, установленной для металлов. Рассмотрим изменение состояния металлической поверхности при одном выбранном методе нанесения ЛКМ, например электро-осаждения. В работе была показана эффективность данного метода для получения на металлах межслойной изоляции в микросхемах высокой степени интеграции, диэлектрических пленок в микросхемах сверхвысокочастотного диапазона и полимерных электроизоляционных покрытий для тепловыделения (блоки питания). Качество электрофоретического покрытия зависит от состояния металлической поверхности. Реальная поверхность металла представляет собой сложную систему адсорбционных слоев (рис.). Их состав и структура определяют такие важнейшие поверхностные свойства металлов (сплавов), как электродный потенциал, электрическое сопротивление, шероховатость, краевой угол смачивания.
Для примера рассмотрим изменение поверхностных свойств алюминиевого сплава АМг5м, в частности потенциала начала растворения электрода (Дф, электрического сопротивления и параметров шероховатости поверхности при различных способах ее механохимической обработки.
Основным критерием состояния алюминиевой поверхности был выбран потенциал начала растворения металла, определяемый потенцио-статическим методом (а. с. 658461 СССР). Этот метод отличается высокой точностью и воспроизводимостью результатов: относительная погрешность измерений для 10 параллельных образцов не превышала 2 %.
Потенциостат (рис.) состоит из источника задающего напряжения с высокоомным вольтметром 2, усилителя 3, электрохимической ячейки типа ЯСЭ с ацетатным буфером 4, миллиамперметра 5, а также помещенных в ячейку хлорсеребряного электрода сравнения 6, исследуемого рабочего электрода 7 и вспомогательного платинового электрода 8.
1 естественным оксидным слоем
Вспомогательный электрод 8 служит для пропускания тока через систему исследуемый электрод — буферный раствор. В качестве исследуемого электрода 7 в электрохимическую ячейку 4 помещают образец металла (сплава) с удаленным покрытием, выполненный в виде лопатки площадью 1 см2. Буферным раствором является эквимолярнай смесь 0,1 н. раствора уксусной кислоты и 0,1 н. раствора ацетата натрия в 3 %-м растворе хлорида натрия с рН = 4,1. В результате проведения серии опытов была установлена высокая стабильность данного состава и хорошая воспроизводимость результатов при незначительной скорости химического растворения металла. В частности, после измерения электродных потенциалов (площадью 200 см2 в ОД л буферного раствора) содержание алюминия в растворе составляло всего 0,0634 г/л. Сущность измерений заключается в том, что при потенциостатической поляризации с помощью источника задающего напряжение 1 поддерживают постоянный потенциал исследуемого электрода 7, определяя силу тока как функцию потенциала. Ток в цепи поляризации регистрируют с помощью миллиамперметра 5. По полученным значениям строят зависимость потенциал — плотность тока и методом касательных находят значение потенциала начала растворения металлического электрода ip.
Для выбора оптимального способа подготовки алюминиевой поверхности были сняты анодные потенциостатические поляризационные кривые образцов сплава АМг5м с естественным оксидным слоем и очищенной механическим способом поверхностью (рис.). Соответствующие им значения потенциалов начала растворения электрода {р и д,р можно условно считать верхней и нижней границами области активно-пассивного состояния алюминиевой поверхности. Это предположение подтверждается и тем, что при наличии на металле толстого естественного оксидного слоя обеспечивается наиболее устойчивое пассивное состояние алюминиевого сплава АМг5м (нр = —676 мВ) и не происходит электро-осаждения водорастворимой эмали В-ЭП-2100 (см. табл. 4). Наоборот, при удалении оксидного слоя механическим способом поверхность значительно активируется (<^р = —736 мВ), но число активных центров на образце, по-видимому, невелико и процесс электро-осаждения протекает с незначительной скоростью.
В области потенциалов средней точки (<рСр= OAip + ¥>нр) /2 = —706 ±10 мВ) обеспечивается максимальная скорость осаждения эмали, вероятно, за счет создания оптимальной пассивности и изоляции наиболее активных 20
центров поверхности образцов. Максимально приближаются к </>ср потенциалы образцов, подвергнутых химическому оксидированию, фторид- ному оксидированию и фосфатировання концентратом КФ-1.
Анализ электронно-микроскопических снимков поверхности и результатов климатических испытаний образцов свидетельствует о высоком качестве электрофоретических покрытий, полученных на поверхности сплава АМг5м, подготовленной указанными выше способами.
Эти же способы могут быть рекомендованы и для подготовки поверхности металлических оснований и проводников ПП, а также микроэлектронных устройств перед нанесением ЛКМ.