Достоинства и недостатки методов получения покрытий из газовой фазы
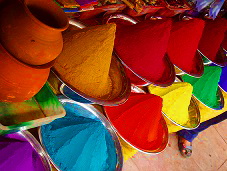
Развитие техники микроминиатюризации и поверхностного монтажа позволило резко снизить размеры и массу РЭС, значительно продвинуть работы по тонкопленочной технологии получения защитных и специальных покрытий. Одно из наиболее перспективных направлений этих работ - получение тонких (до 20 мкм) органических покрытий из газовой фазы. Для формирования таких покрытий и пленок в настоящее время применяют различные методы, в которых используется энергия излучения заряженной частицы или тепловая энергия. При этом покрытия можно получать как из мономеров, так и из полимеров.
Методы получения покрытий из газовой фазы можно классифицировать следующим образом:
1) электронная или лазерная бомбардировка мономерно-олигомерных или полимерных систем;
2) облучение поверхности УФ-лучамив присутствии паров мономера;
3) плазмохимические методы;
4) термическое разложение в вакууме низкомолекулярных органических веществ или полимеров с последующей их конденсацией на поверхности изделия (пиролитическая полимеризация).
Получаемые перечисленными методами тонкие полимерные покры-: тия характеризуются сочетанием высоких электрофизических, оптических, термических и других свойств. За рубежом они широко применяются, особенно в микроэлектронике. Такие покрытия используются также для противокоррозионной защиты и герметизации полупроводниковых приборов, интегральных схем, ЭМ1 и ЭМ2.
В случае применения покрытий, получаемых из газовой фазы, для влаго-защиты РЭС выбор ЛКМ и метода их нанесения представляет значительную трудность, поскольку ограничивается следующими факторами:
1) недостатки технологии влаго-защиты лаками — неравномерность и многослойность покрытий, токсичность и пожароопасность производства и др.;
2) температура формирования покрытия не должна превышать 70 °С;
3) отрицательное влияние высоких электрических напряжений на ЭРЭ и ИЭТ, в том числе накопление на изделиях поверхностных зарядов (плазмохимические методы, энергия ускоренных электронов);
4) теневые и краевые эффекты излучения под навесными ЭРЭ и ИЭТ (УФ-излучение);
5) сложное и дорогостоящее аппаратурное оформление процесса.
Наиболее перспективным методом получения покрытий является термическое разложение органических соединений, хотя и довольно ограниченного круга. Для РЭС и МСБ наибольший интерес представляют поли-л-ксилиленовые покрытия (ППКП), которые формируются в вакууме на поверхности изделия в результате пиролиза «-ксилола или порошкообразного дииксилилена. Широко известно применение ППКП (за рубежом торговое название „парилен”) для защиты ПП в авиакосмической и радиоэлектронной промышленности. Обладая высокими защитными и диэлектрическими свойствами, ППКП выполняют еще одну важную функцию — плотно охватывая „козырьки”, образовавшиеся на краях печатных проводников при боковом подтравливай, они предотвращают их обламывание и короткое замыкание между соседними проводниками.
Широкий интерес к ППКП обусловлен следующими их достоинствами:
1) твердое покрытие формируется непосредственно из газообразного мономера, минуя жидкую фазу, благодаря чему исключаются проблемы вязкости и жизнеспособности ЛКМ, поверхностного натяжения и внутренних напряжений покрытий;
2) покрытие образуется одновременно и равномерной толщины по всей поверхности изделия, независимо от его профиля;
3) однослойное сплошное покрытие получается за сравнительно короткое время (до 20 мин) и не содержит точечных отверстий, микропустот;
4) покрытие формируется при комнатной температуре, что гарантирует сохранность работоспособности ИЭТ и возможность проведения контрольно-регулировочных работ и климатических испытаний непосредственно после окончания процесса формирования ППКП;
5) отсутствие остатков катализаторов и следов растворителей в ППКП не вызывает появления токов утечки и коррозии, обеспечивает наибольшее электрическое сопротивление;
6) покрытие отличается стойкостью к органическим растворителям, корродирующим жидкостям и газам (соляная и азотная кислоты, кислород, хлор и др.) и по комплексу свойств ППКП толщиной 6,3—38 мкм эквивалентны лаковым покрытиям толщиной 50—125 мкм;
7) для ремонта ППКП в полевых условиях можно применять низковязкие эпоксидные и полиуретановые лаки;
8) низкая токсичность, пожаро и взрывоопасность производства, что позволяет эксплуатировать СТО непосредственно в сборочных цехах;
9) при серийном производстве процесс формирования ППКП может быть полностью автоматизирован и при этом исключены безвозвратные потери и вредные выбросы материалов в окружающую среду.
К недостаткам ППКП можно отнести их низкую адгезию к цветным металлам (никель, серебро, золото) и некоторым материалам с высоким классом чистоты покрываемой поверхности (например, ситалл), а также недостаточную стойкость к солнечному излучению.
За рубежом имеется ряд публикаций с рекомендациями по устранению указанных недостатков [например, пат. 4173664 США]. Наиболее интенсивные исследования проводят фирмы Union Carbide Corp. (США), Esso Research and lingin (ClliA), Du Pont de Nemours (США).Mylar (США), Imperial Chemical Industrie (Великобритания), Teijin Ltd (Япония), Asaki Chemical Ind. Со (Япония), „Мацусита Дэнки сангё” (Япония), „Тойота дзидоэя когё” (Япония). Oven (Швейцарии) и др. [72-74]. Аналогичные работы проводятся в СССР.
Следует отметить, что поли-л-ксилилен является в настоящее время единственным циклическим пленкообразователем, способным к пиролитической полимеризации с образованием тонких и сплошных пленок и покрытий. По структуре — это (в зависимости от технологии получения) аморфный или кристаллический полимер, для повышения адгезии которого применяются различные способы активации покрываемой поверхности.